Case Study: Energy Savings in Manufacturing through Strategic Budgeting
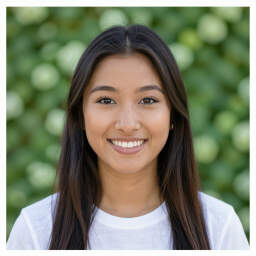
This article explores a real-world case study on energy savings in manufacturing, highlighting how strategic budgeting led to significant reductions in costs and environmental impact. It covers practical strategies and emerging trends for energy efficiency.
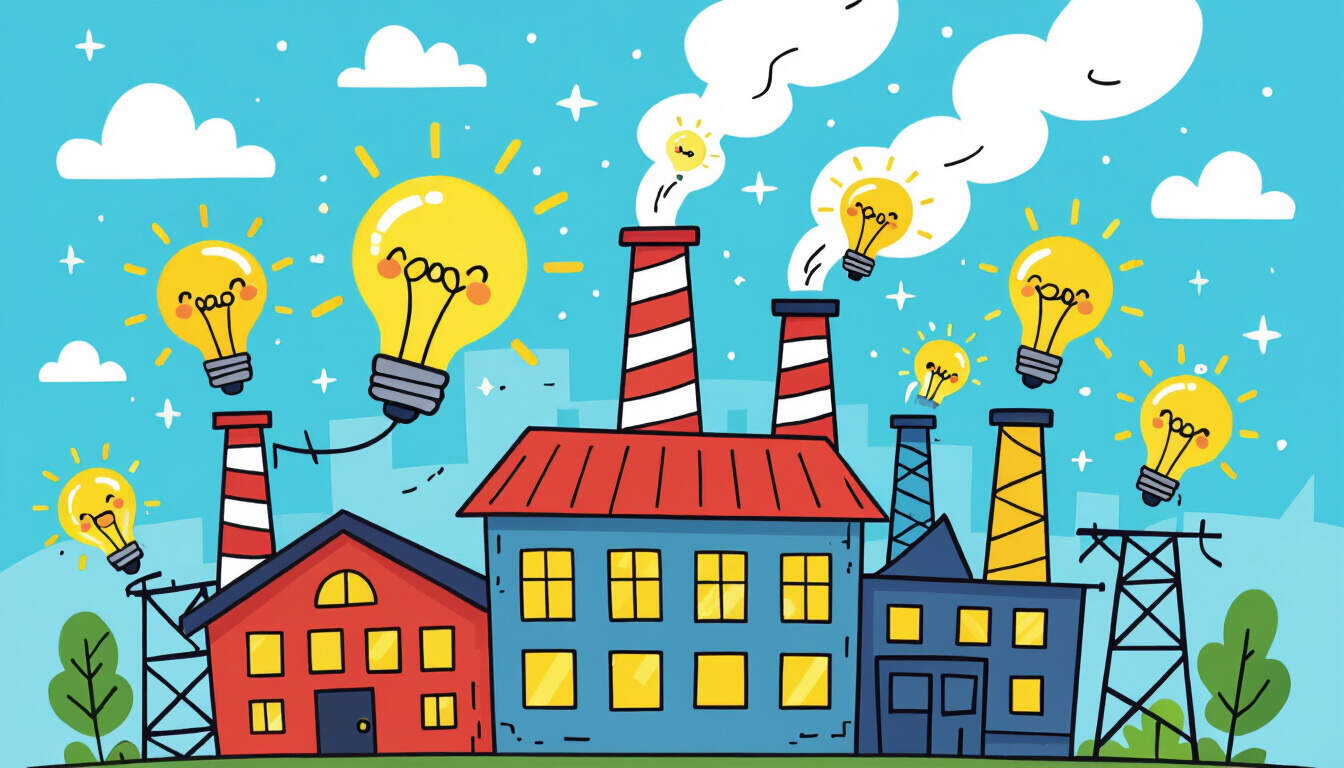
Energy savings play a crucial role in modern manufacturing, helping businesses reduce operational costs while supporting sustainability goals. In this case, a mid-sized manufacturing plant focused on energy savings by implementing a structured budgeting approach.
The plant, which produces automotive parts, faced rising energy expenses that affected profitability. By analyzing usage patterns, the team identified key areas for improvement, such as outdated machinery and inefficient lighting systems. This led to a targeted initiative where investments were prioritized based on potential returns.
One effective strategy involved upgrading to energy-efficient equipment. For instance, replacing old motors with variable speed drives resulted in immediate reductions in electricity use. The plant's management allocated funds specifically for these upgrades, ensuring that every dollar spent contributed to long-term savings.
In the case study, the manufacturing facility achieved a 20% reduction in energy consumption within the first year. This success stemmed from regular monitoring and adjustments, allowing the team to track progress and make data-driven decisions. Manufacturing efficiency improved as a result, with less downtime and better overall performance.
Practical strategies like this can be applied across various industries. For example, conducting energy audits helps identify waste and opportunities for optimization. In the plant's scenario, simple changes, such as installing sensors for automated lighting, yielded surprising results without major disruptions.
Emerging trends in energy efficiency are also shaping the future of manufacturing. Innovations like smart grids and renewable integration offer new ways to manage resources. The case study plant began exploring solar panels as a cost-effective addition, which aligned with broader sustainability efforts.
Key Lessons from the Case Study
From this example, several insights emerge:
- First, early investment in energy-efficient technologies can lead to substantial cost reductions.
- Second, involving employees in the process fosters a culture of conservation.
- Regular reviews of energy data ensure that strategies remain effective over time.
The manufacturing sector continues to evolve, with more businesses adopting these practices. For instance, another plant in the same region reported similar gains by focusing on waste heat recovery systems. These real-world applications demonstrate the value of proactive measures.
Strategies for Implementation
To replicate such success, businesses can follow a step-by-step approach:
- Assess current energy usage to pinpoint inefficiencies.
- Set clear budgeting goals based on projected savings.
- Invest in training for staff to maintain new systems.
- Monitor outcomes and adjust plans as needed.
This structured method not only cuts costs but also enhances competitiveness. In the case of the automotive parts plant, these steps transformed operations and set a benchmark for others.
Looking ahead, trends like digital twins for simulation and predictive maintenance are gaining traction. These tools allow manufacturers to forecast energy needs and optimize budgets more precisely. The case study highlights how forward-thinking approaches can drive ongoing improvements.
In conclusion, the case study underscores the benefits of strategic energy budgeting in manufacturing. By focusing on practical actions and staying informed about new developments, businesses can achieve meaningful energy efficiency gains. This not only boosts the bottom line but also contributes to a more sustainable future.